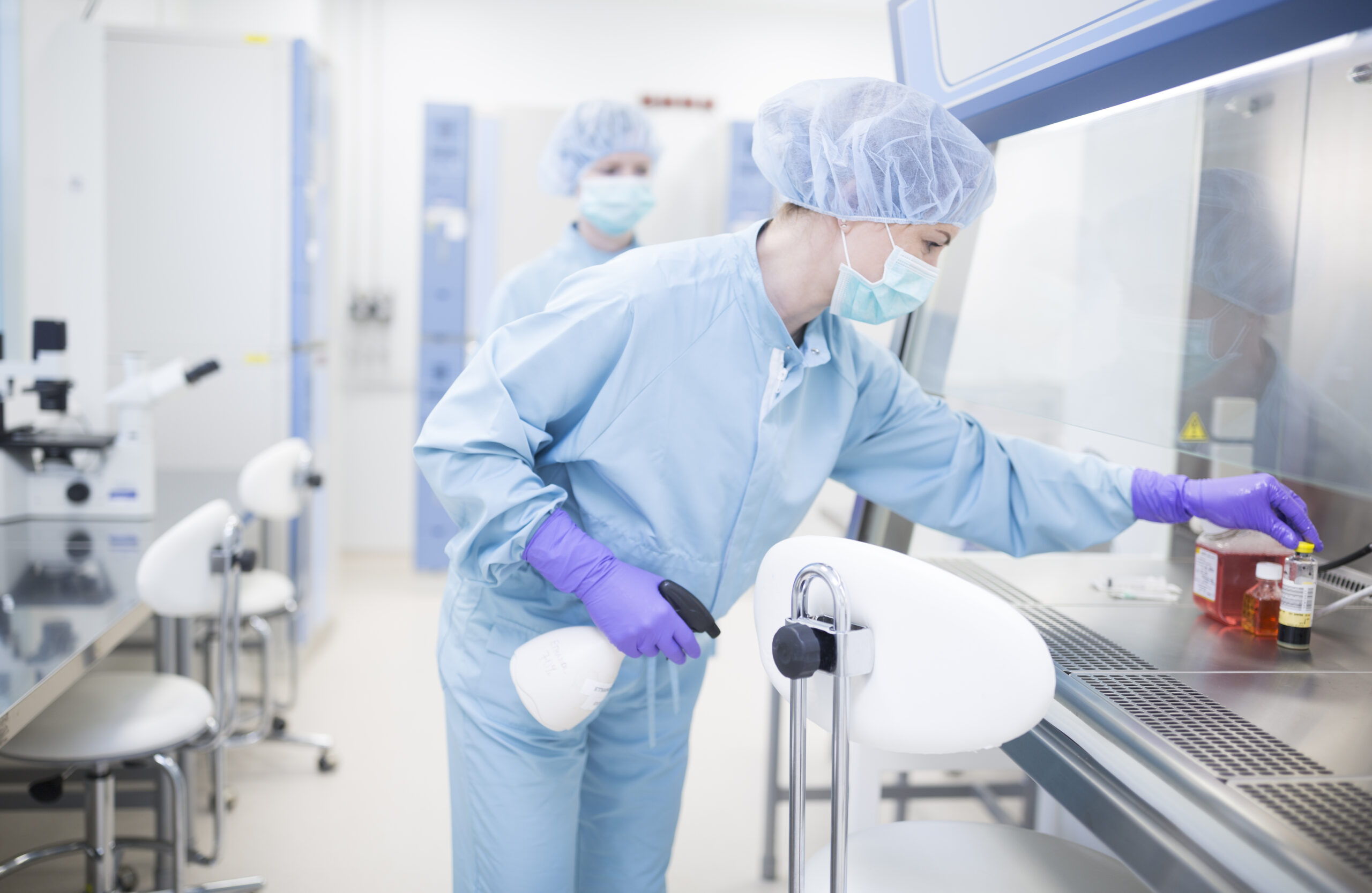
In the life sciences industry, cleanrooms are required for everything from drug development to the production of sterile medical tools. They preserve the integrity of scientific research and can also help commercial enterprises ensure high-quality manufacturing.
Keeping cleanrooms sterile isn’t just a matter of ongoing maintenance. It starts with a series of design decisions, including everything from air filtration to materials selection.
Before you break ground on your next cleanroom, you should be aware of what to consider. In this post, we’ll break down everything you need to know, including:
- Major Design Considerations
- The Difference in Modular vs. Traditional Construction
- Ongoing Maintenance Tips
We’ll also take a look at some current and future trends designers should know about.
Major Design Considerations for Life Sciences Cleanrooms
Cleanrooms in life sciences facilities are defined by their ability to control particulate contamination. This involves a combination of air filtering, efficient ventilation, and smart materials choices.
Air Filtration
Minimizing air particulates is primarily achieved through sophisticated air filtration systems, so you’ll want to start here.
HEPA filters are the gold standard it comes to air filtration. The most efficient systems can trap up to 99.97% of particles that are 0.3 microns or larger in diameter.
HEPA filters also move air rapidly, ensuring any airborne contamination within a room is short-lived. The best HEPA filters can recirculate the air in a room up to 600 times per hour. (A normal, unrestricted room would only change air around 10 times per hour.)
Cleanrooms also maintain positive pressure in relation to outer rooms. This ensures that air always moves out of the room, even if doorways are open for a brief period of time.
Air filtration for cleanroom is governed by the ISO standard 14644-1, and is measured in terms of the concentration of airborne particles.
Ventilation Efficiency
Maintaining optimal air quality extends beyond filtering to how air is circulated within the cleanroom.
The design of the ventilation system is crucial, with air change rates (how frequently the air in the room is replaced) and airflow patterns (laminar or turbulent) playing key roles in contaminant control.
For more critical applications, the air change should be as frequent as every few minutes. This helps ensure that any contaminants introduced are swiftly removed.
Moreover, the airflow patterns should be designed to minimize dead spots where contaminants might accumulate. Some cleanrooms employ unidirectional airflow to further reduce risks of contamination.
Material and Structural Choices
Wall systems and flooring must not only support the sterile conditions but also withstand rigorous cleaning protocols.
Common materials include vinyl flooring, which is favored for its ease of maintenance and resistance to contaminants, and modular wall panels, which offer versatility and ease of installation.
These materials are specifically chosen to reduce particle shedding and resist microbial growth, ensuring the integrity of the cleanroom environment.
Once you understand the broad strokes of life sciences cleanroom design, you can begin to examine the finer details.
Modular vs. Traditional Construction
While modular cleanrooms and laboratories may present a higher initial investment, they can offer advantages when it comes to expanding and changing your cleanroom over time. However, modular construction pieces need to be pre-fabricated and shipped to site, potentially leading to project delays.
Traditional stick-built cleanrooms are constructed on-site using conventional building materials such as chemically resistant FRP, steel, or vinyl. This method can be more efficient to build but can be difficult to expand later. Because new technologies and processes are constantly emerging in the life sciences and healthcare industries, your design/build firm should be involved early in the planning process and help you understand which method is right for your project.
Ultimately, you’ll want to go with a design that makes the most sense for your needs while taking into consideration the materials and supplies that are readily available.
Thoughtful Design Saves Money in the Long Run
Effective cleanroom design focuses on durability, adaptability, and operational efficiency. These factors are crucial for maintaining sterility standards and accommodating rapid technological advancements.
Focusing on materials and layouts that enhance operational longevity and adaptability brings considerable cost benefits:
- Select materials like coated steel or premium aluminum to resist wear and facilitate easy maintenance. Their longevity reduces the need for frequent renovations, cutting long-term costs.
- A forward-thinking layout can adapt to future technology shifts or process expansions with minimal disruption. This adaptability is critical in the dynamic field of life sciences.
- Designing for efficiency from the outset minimizes ongoing operational costs. Where available, modular features that support easy upgrades or expansions can prevent costly downtimes.
Balanced investments in these areas lead to a cleanroom that functions effectively from day one.
Current Life Sciences Cleanroom Trends and Tomorrow’s Innovations
Cleanroom and laboratory design is always evolving, driven in part by advances in technology but also by shifting regulatory standards.
AI Is Making its Way into Life Sciences Cleanrooms
The integration of smart technologies, such as Internet of Things (IoT) sensors, is enhancing the ability to monitor and control life sciences cleanrooms more precisely.
These technologies provide real-time data on environmental conditions, allowing for immediate adjustments to maintain strict cleanliness standards. By integrating AI, they can also offer predictive analytics to foresee potential failures or contamination risks before they occur. This can lead to preemptive maintenance and operational adjustments that enhance efficiency and safety.
New Materials and Construction Techniques
Modern cleanrooms are also integrating the latest materials and construction breakthroughs to create the most efficient cleanrooms possible. This includes:
- Epoxy and vinyl flooring that are resistant to chemicals, easy to clean, and anti-static. These cost-effective floors are seamless and non-porous, making them a perfect low-cost option for cleanrooms.
- Modular wall panels are typically made from materials like aluminum, steel, or plastic, which makes them easy to install, modify, and maintain.
- Techniques like Building Information Modeling (BIM) and 3D modeling are becoming more common in cleanroom construction. These technologies help visualize the ending solution before construction begins, allowing for necessary modifications to optimize cleanroom functionality.
When new innovations are ready to help your research team take your company to the next level, proper design and an eye on the horizon can ensure you’re ready to move quickly.
Key Interiors Can Help Design Your Next Life Sciences Cleanroom
The design and construction of cleanrooms in the life sciences industry influence not only the effectiveness of operations but also the quality of outcomes.
Designers need to know about stringent air filtration standards, smart modular construction options, and the cleanrooms of tomorrow.
If you are planning to design and construct a cleanroom, Key Interiors can offer the expertise needed to ensure that your facility meets all required standards and is equipped for future advancements.
Our team is ready to help you create a clean room that not only meets today’s standards but is also prepared for tomorrow’s challenges.
Contact Key Interiors today to ensure your next cleanroom project is a success from the ground up.